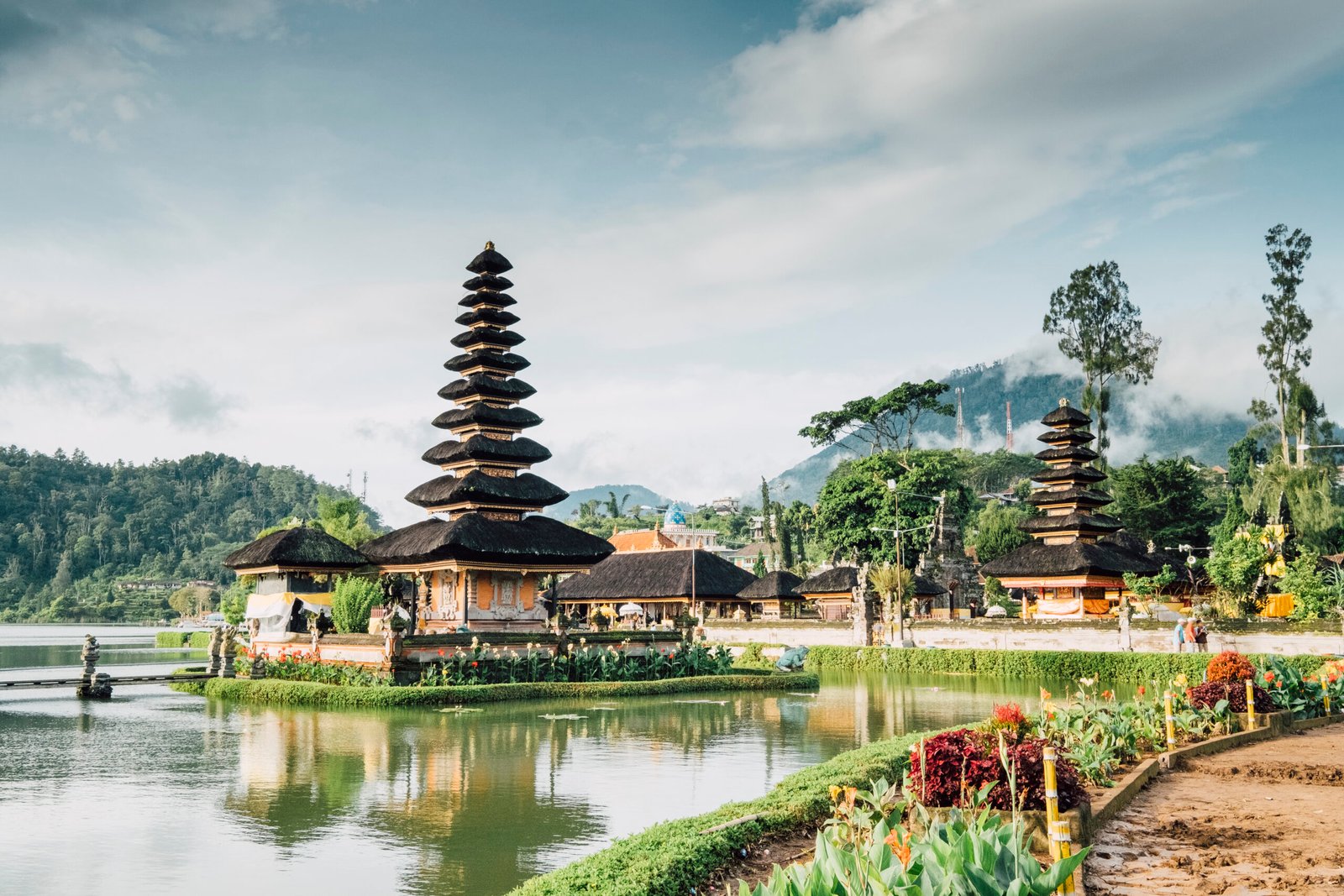
Maintenance Auditing, Benchmarking & Improvement
In today’s industrial and operational environments, maintaining equipment and facilities at peak performance is crucial for minimizing downtime, reducing costs, and ensuring safety. This course provides a comprehensive approach to maintenance auditing, benchmarking, and continuous improvement to help businesses achieve world-class maintenance standards.
Participants will learn audit methodologies, key performance indicators (KPIs), benchmarking techniques, and improvement strategies to enhance maintenance processes. The course incorporates real-world case studies, practical exercises, and expert-led discussions to ensure hands-on learning and effective implementation.
Maintenance Auditing, Benchmarking & Improvement objectives:
By the end of this course, participants will be able to:
- Understand maintenance auditing frameworks and methodologies.
- Develop effective maintenance audit plans and conduct assessments.
- Utilize benchmarking techniques to compare maintenance performance with industry standards.
- Identify areas for improvement in maintenance processes.
- Implement best practices in predictive, preventive, and corrective maintenance.
- Optimize maintenance costs and resource allocation.
- Enhance overall reliability, efficiency, and safety in maintenance operations.
Who Should Attend:
This course is designed for:
- Maintenance managers and supervisors seeking to enhance efficiency.
- Operations and plant managers responsible for asset management.
- Engineers and technicians involved in maintenance activities.
- Reliability and asset management professionals.
- Auditors and quality assurance personnel in maintenance.
- Business owners and facility managers looking to optimize maintenance processes.
Course Outline
Day 1: Introduction to Maintenance Auditing
- Fundamentals of maintenance management and auditing.
- Types of maintenance audits (internal vs. external).
- Key elements of a successful maintenance audit.
- Maintenance standards and regulations overview (ISO 55000, PAS 55).
- Case study: Best practices in maintenance auditing.
Day 2: Designing and Conducting Maintenance Audits
- Steps in preparing for a maintenance audit.
- Developing a maintenance audit checklist.
- Data collection techniques for effective auditing.
- Identifying gaps in maintenance processes.
- Practical exercise: Conducting a sample maintenance audit.
Day 3: Benchmarking in Maintenance Performance
- Introduction to benchmarking in maintenance.
- Key Performance Indicators (KPIs) in maintenance auditing.
- Internal vs. external benchmarking.
- Using industry benchmarks to measure maintenance performance.
- Case study analysis: Global benchmarking success stories.
Day 4: Identifying and Implementing Improvement Strategies
- Root Cause Analysis (RCA) for maintenance failures.
- Applying Lean Maintenance and Six Sigma for process improvement.
- Optimizing maintenance workflows for efficiency.
- Workshop: Identifying improvement areas in real-world scenarios.
Day 5: Predictive, Preventive & Corrective Maintenance Optimization
- Understanding Predictive Maintenance (PdM) and its role.
- Best practices in Preventive Maintenance (PM) programs.
- Integrating Corrective Maintenance (CM) with improvement strategies.
- Hands-on exercise: Developing a maintenance improvement plan.
Day 6: Asset Reliability and Maintenance Strategy Development
- Reliability-Centered Maintenance (RCM) and its importance.
- Developing a Total Productive Maintenance (TPM) strategy.
- Cost-benefit analysis of different maintenance approaches.
- Implementing a risk-based maintenance strategy.
- Group discussion: Best approaches for sustainable maintenance.
Day 7: Technology and Digital Tools in Maintenance Improvement
- Role of CMMS (Computerized Maintenance Management Systems).
- Using IoT, AI, and Big Data for predictive maintenance.
- Implementing automation in maintenance auditing.
- Case study: Digital transformation in maintenance.
Day 8: Financial and Cost Analysis in Maintenance Management
- Budgeting and cost control for maintenance.
- Calculating Return on Investment (ROI) in maintenance improvement.
- Justifying maintenance investments to stakeholders.
- Exercise: Creating a cost-efficient maintenance improvement plan.
Day 9: Continuous Improvement and Performance Evaluation
- Setting up a Continuous Improvement (Kaizen) framework.
- Evaluating long-term effectiveness of maintenance improvements.
- Conducting post-audit follow-ups and reassessments.
- Workshop: Developing a customized maintenance improvement roadmap.
Day 10: Capstone Project & Final Presentations
- Participants will work in teams to audit a real or simulated maintenance process, analyze benchmarking data, and propose an improvement plan.
- The project will be presented to instructors and peers for evaluation and feedback.
- Certification, Q&A, and final recommendations for practical application.